Dust at work: preventing lung disease
Thousands of cases of irreversible lung diseases, such as silicosis, are reported annually. Caused by exposure to dust at work, such diseases are preventable, but tragically can be life-changing or even result in loss of life. In this briefing, Claire Deacon PhD, Health and Safety Trainer at International Workplace looks at causes and control measures to prevent such diseases.
The HSE states that close to 12,000 deaths are caused by lung disease annually, related to past exposures at work. A total of 34% of deaths are a result of chronic obstructive pulmonary disease (COPD).
Health issues historically receive less attention than safety issues. However, if hazards are identified and the degree of exposure identified, appropriate and reliable controls can be applied.
Causes
Silica, known as Respirable Crystalline Silica (RCS) is generated from a wide range of materials as silica is found in stone, rock, sand and clay. The main sources of silica are contained in sandstone, gritstone and quartzite (made up of more than 70% silica). Concrete and mortar are known to contain between 25% and 70% silica, with shale including from 40% to 60%.
The HSE reports that there are numerous occupations that expose workers to high levels of silica. Key occupations include construction work and stonework. Recent research indicates that the use of artificial stone, commonly used as kitchen and bathroom counters, has accelerated the exposure levels of RCS.
Exposure
RCS is produced by a range of work tasks, including sandblasting, drilling, brick cutting, glass manufacturing, stonework and various construction activities. These activities create dust particles of various sizes, and the smaller they are, the more lethal they are. Of major concern are those particles of respirable size, which means they get into the lungs, bypassing the cilia in the nose and upper respiratory tract that cause us to sneeze and cough when exposed to dust.
Exposure limits
Most countries have set legal limits of exposure, both in terms of time and level/quantity. Such limits are called workplace exposure limits (WEL) or occupational exposure limits (OEL). If these limits are exceeded the substances are known to cause disease. The UK sets the limits as part of the Control of Substances Hazardous to Health Regulations 2002 (COSSH). In the UK, the current acceptable limit in the atmosphere is 0.1mg/m3. Exposure (known as the time weighted average (TWA)) is also determined by the number of hours worked, generally a period of eight hours per day, over a 40-hour week. When the TWA and the WEL are exceeded, the employee is at risk. Control of exposure is not stipulated, however the Management Regulations (1999) do require employers to identify what risks exist to their own employees or others who may be exposed during work.
Signs and symptoms of disease
The HSE states that close to 12,000 deaths are caused by lung disease annually, related to past exposures at work. A total of 34% of deaths are as a result of chronic obstructive pulmonary disease (COPD).
It can take up to 40 years after exposure for silicosis to manifest itself, depending on the levels of exposure. Duration of exposure is required to be considered in that the maximum respirable dust level is 0.1mg/m3. Due to such an extended lag/latency period before the disease is diagnosed, many workers are most likely to have stopped work, making it quite difficult to make the connection.
Disease progression is not dependent on further exposure. Once symptoms have started, the disease will continue to develop. It is seldom that progression can be halted, only a lung transplant would be likely to halt any further development.
The core symptom of silicosis is a persistent cough. Shortness of breath and general feelings of weakness and tiredness may be experienced. As the disease progresses, climbing stairs or walking become very difficult and so may result in individuals becoming bedridden. Unfortunately, the individual could be susceptible to other associated life-threatening diseases such as tuberculosis (TB), heart failure, kidney diseases, and further infections which may result in death.
Occupational disease and health surveillance
Where there is a link between what work is being done, and proof that the employee was working in such an environment, any disease related to the exposure would be deemed to be an occupational disease. Occupational diseases are covered by insurances that are legally required in most countries.
Health surveillance looks at occupational exposure and employers’ conduct to identify if there is any evidence of early disease or symptoms. Surveillance could be in the form of periodic questionnaires, lung function tests, and chest X-rays. Health surveillance is carried out by medically-trained professionals, who promote and maintain the wellbeing of employees. Medical records need to be kept for up to 40 years, in a safe and secure environment.
Measuring exposure
Measuring of exposure takes two main approaches. The first is to review all materials and processes that are required to complete tasks. The use of safety data sheets (SDSs) is the first area that needs to be considered. The monitoring of the dust levels would be carried out by an occupational hygienist, who would determine the levels and type of dust. They further assist organisations with the selection of the appropriate personal protective equipment (PPE). Dust measuring is a scientific measure, and the findings would provide a dependable result for employers to work with to determine controls.
Controlling dust
Controls begin with identification. Understanding what is going to be done and how and who will be exposed are all part of the identification process. Using the typical hierarchy of control provides guidance regarding what can be done.
Designers can consider their designs and select materials or finishes that contain lower amounts or no silica. Contractors can add by further interrogating their processes and substituting products and processes. The higher the number of controls and PPE that need to be worn, the more it costs.
Ways to reduce exposure include, among others:
- Less powerful tools that produce less dust;
- Use of water that is sprayed onto the tool to reduce the dust or water suppression; and
- ‘On-tool’ extraction or vacuum systems that can be safely filtered or scrubbed from the atmosphere.
Training and the use of dust masks are further required where RCSs cannot be limited.
Conclusion
The use of products, processes and tools that emit or create dust containing RCSs need to be actively considered. Identification of hazards and knowing the dust levels assist in the selection of alternative products, processes and tools by designers, contractors and general industry. Employees need to be trained regarding the risks, and provided with appropriate PPE where dust cannot be controlled. Heath surveillance and dust monitoring are ways in which risk can be confirmed and exposure to employees controlled.
Further information
International Workplace's Dust and silica exposure training course
[Construction Industry Training Board (CITB](https://www.citb.co.uk/about-citb/partnerships-and-initiatives/construction-dust-partnership/advice-for-employers/))
[Health and Safety Executive: Silicosis. ](https://www.hse.gov.uk/lung-disease/silicosis.htm)
[Health and Safety Executive: Health surveillance for those exposed to respirable crystalline silica (RCS)](https://www.citb.co.uk/about-citb/partnerships-and-initiatives/construction-dust-partnership/advice-for-employers/)
You may also be interested in
RELATED CONTENT
RELATED CONTENT
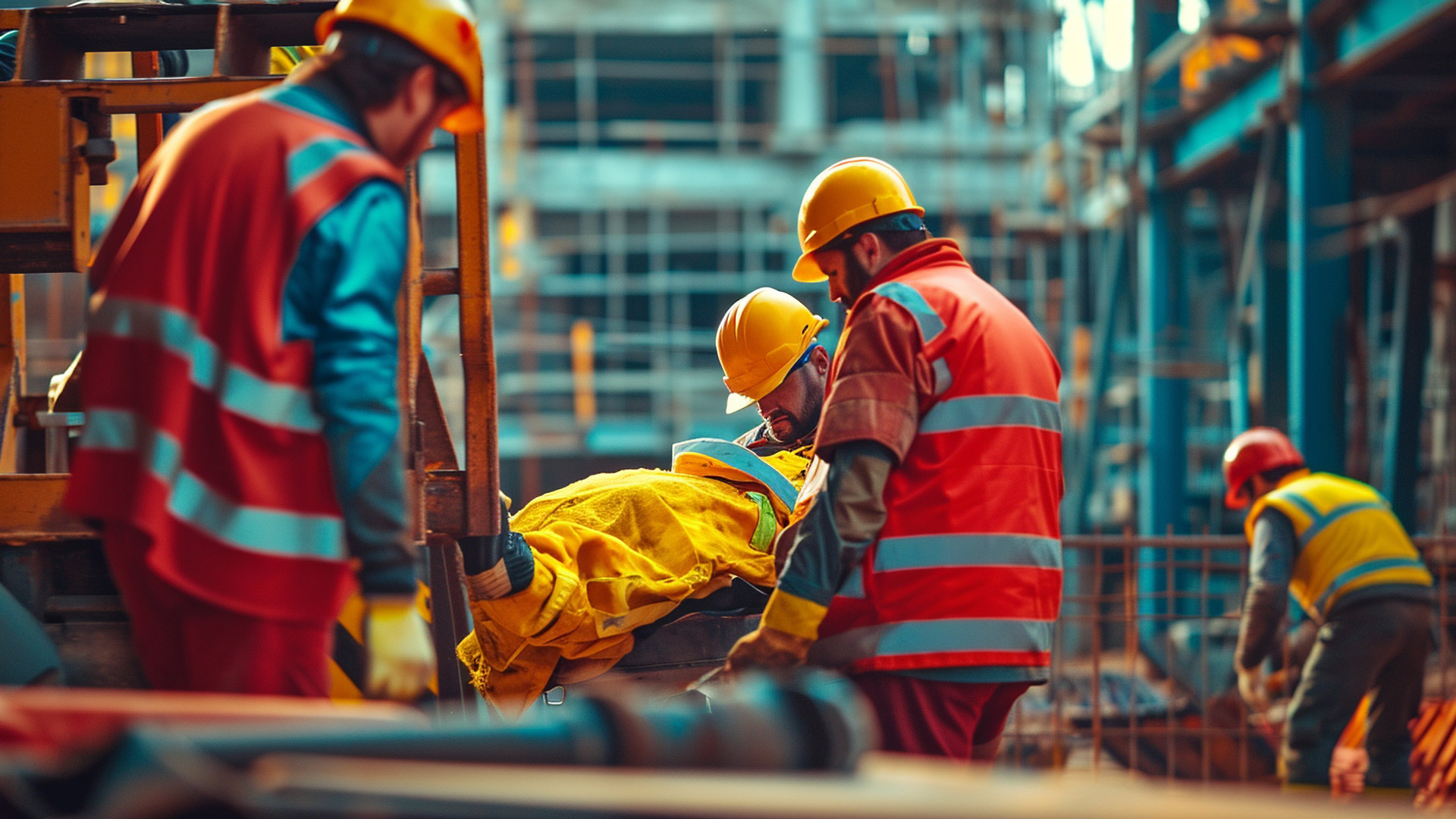
The Accident and incident reporting course helps learners develop skills to deal with the aftermath of an accident or incident.
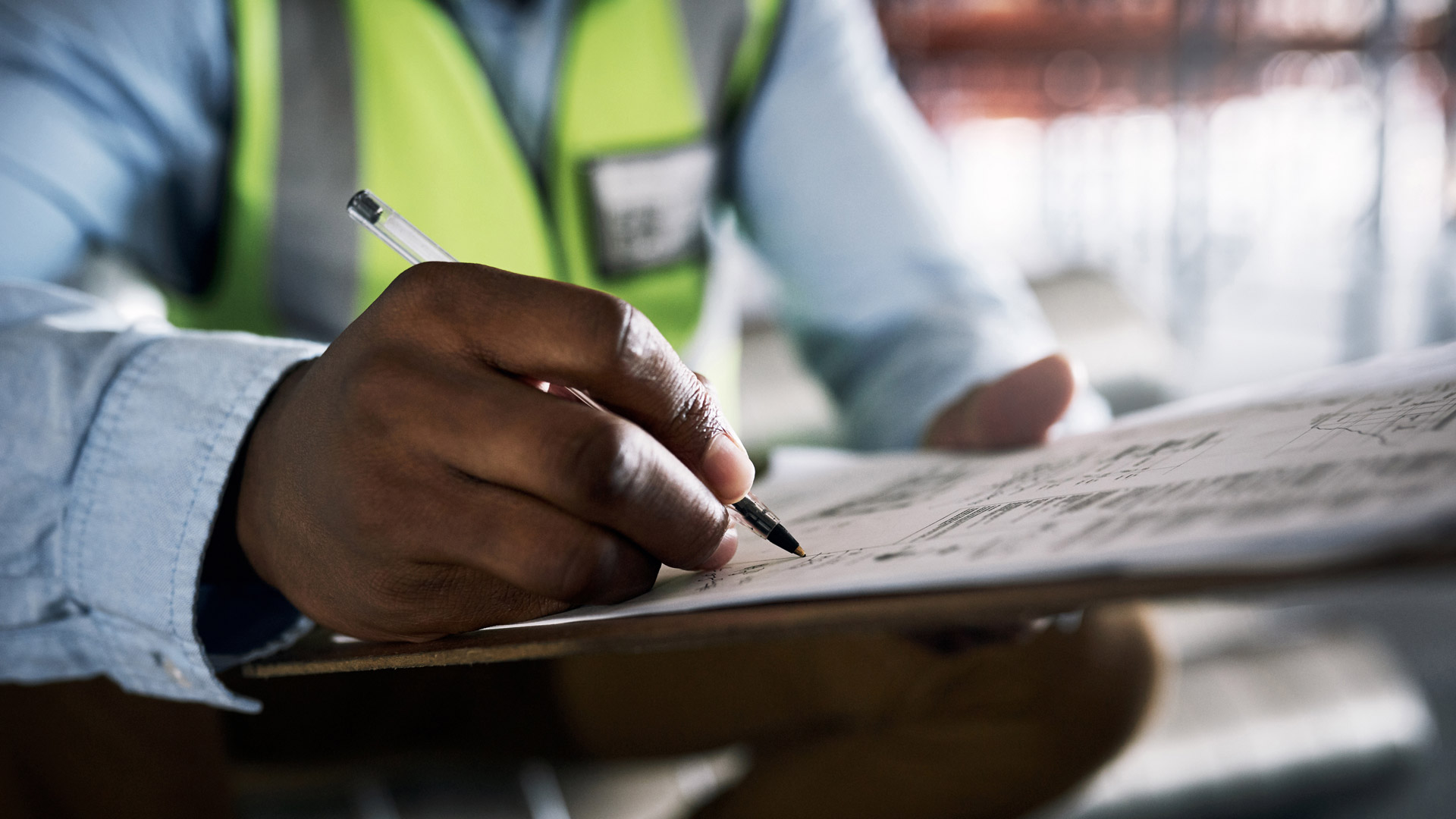
The Risk Assessment and Method Statement (RAMS) course examines the HSE’s recognised five-step approach to risk assessment.
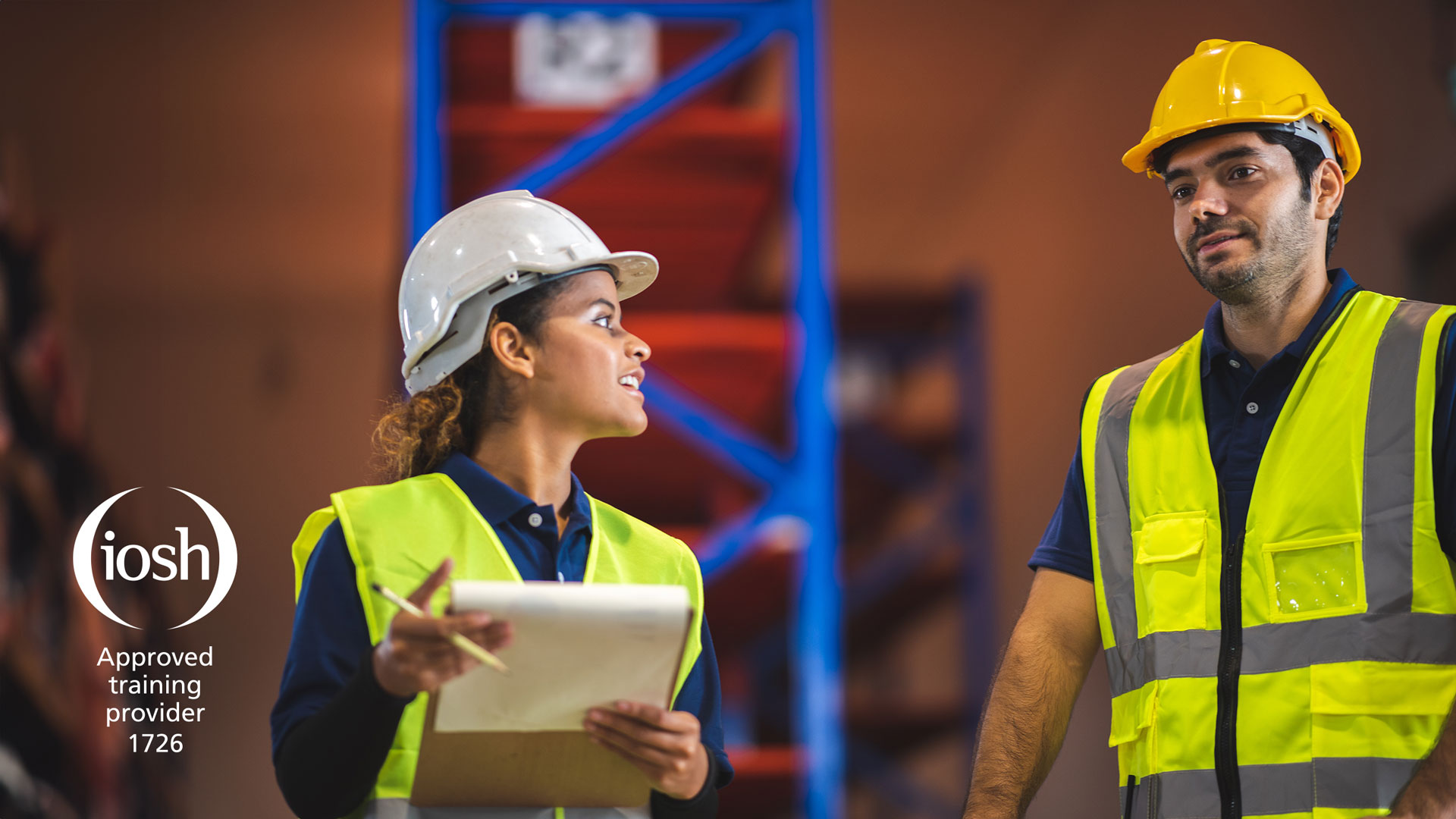
The world’s best-known health and safety certificate, designed for managers and supervisors in any sector or organisation.
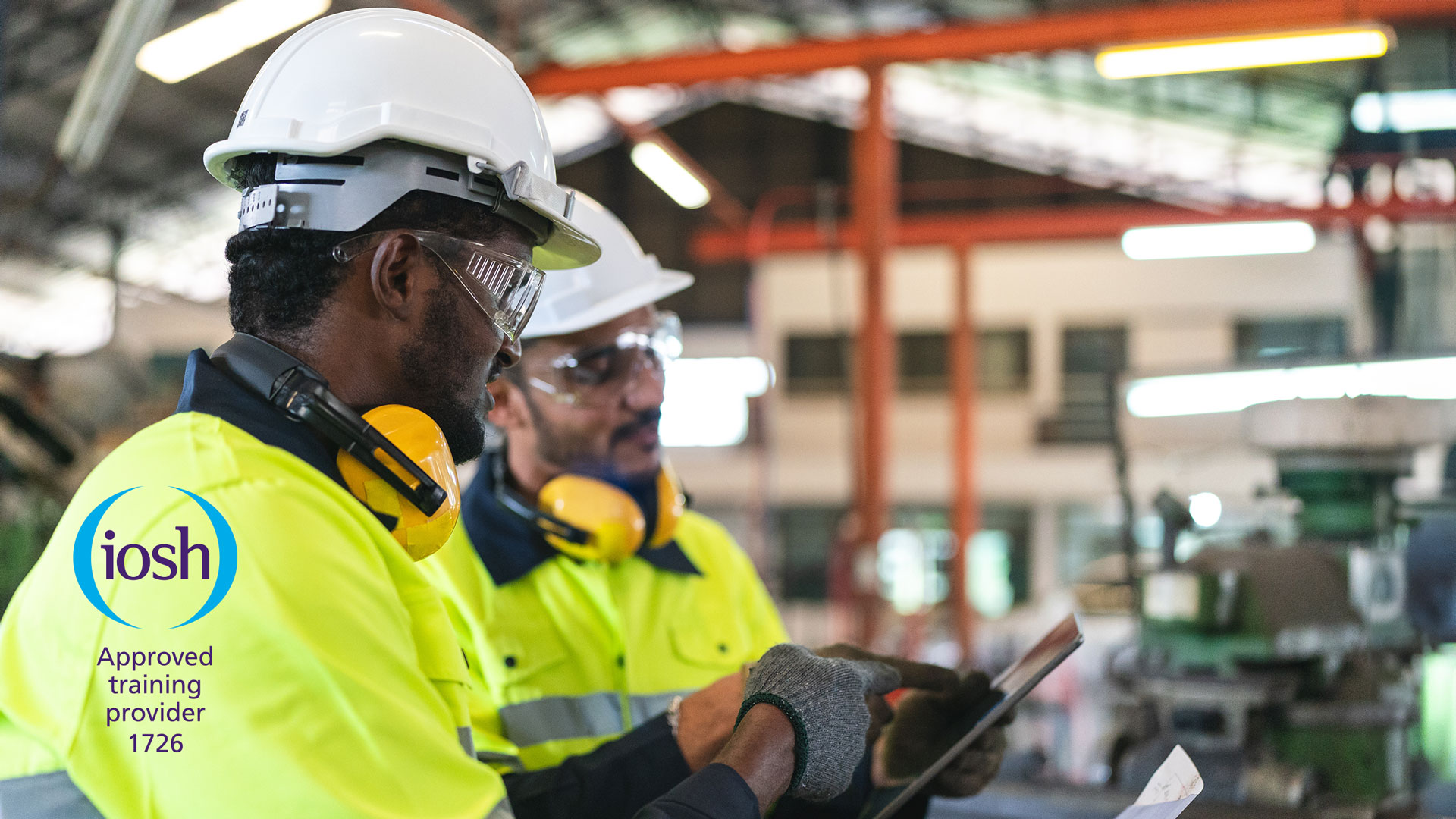
IOSH Working Safely is a one-day introductory health and safety training course for people at any level, in any sector.
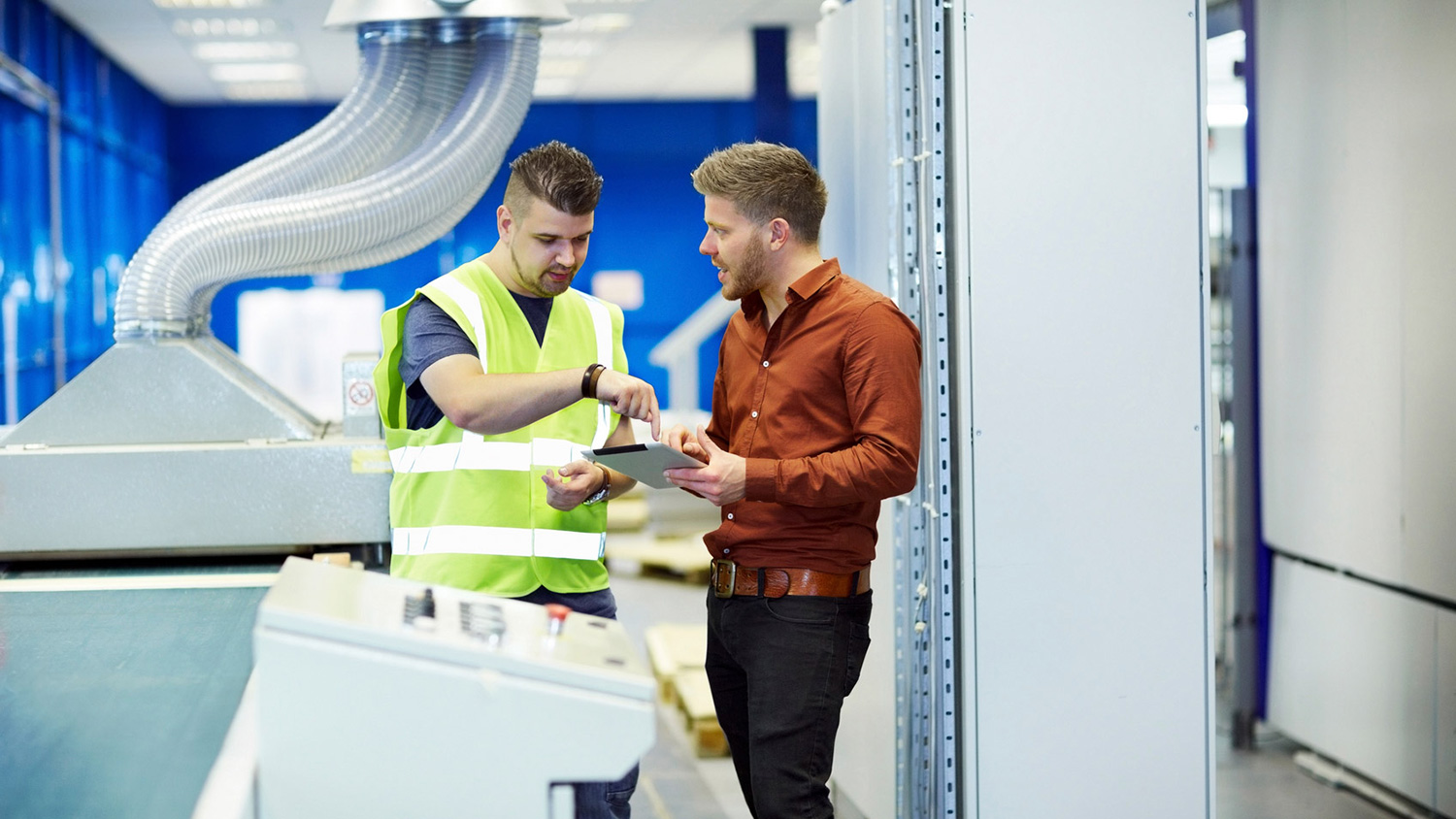
Risk assessments are often the first thing to be reviewed in the event of an accident. Claire Deacon PhD, Health and Safety Trainer with International...
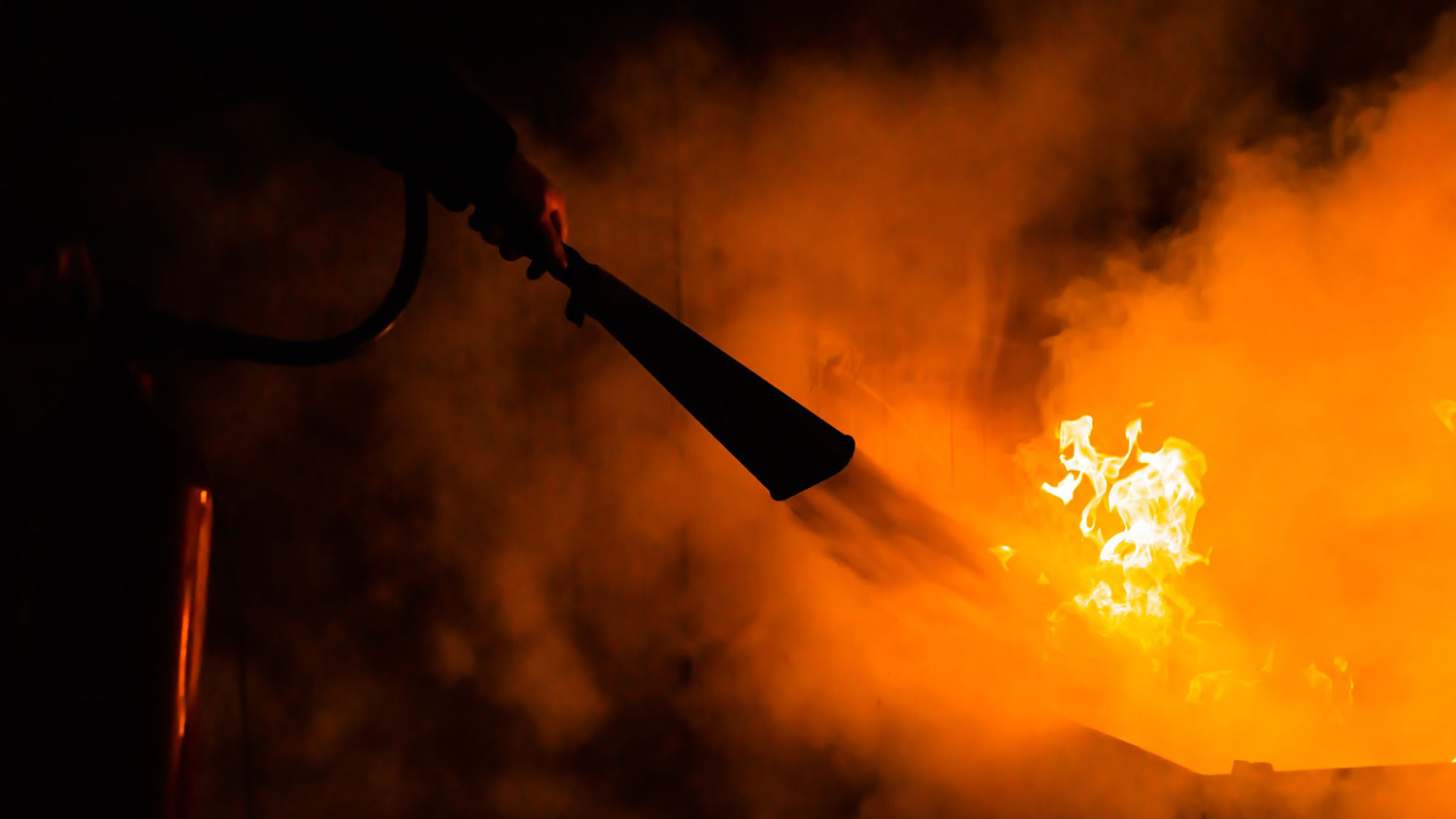
Responsibility for fire risk assessment in the workplace is changing in line with new legislation. In this briefing, John Davidson of security and fir...
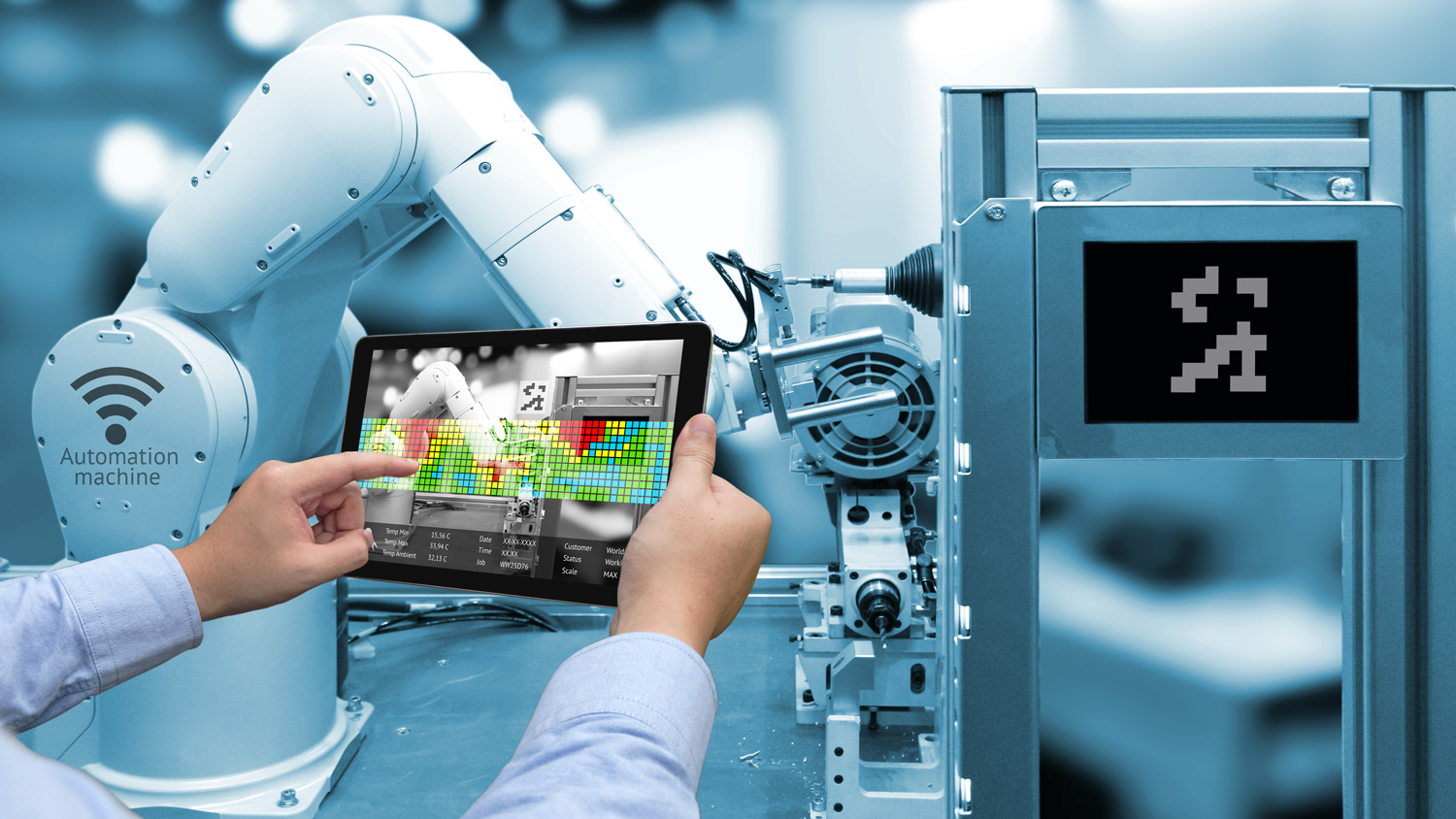
The use of machines in the workplace is nothing new. But, whereas robots were initially built to carry out simple tasks, nowadays artificial intellige...
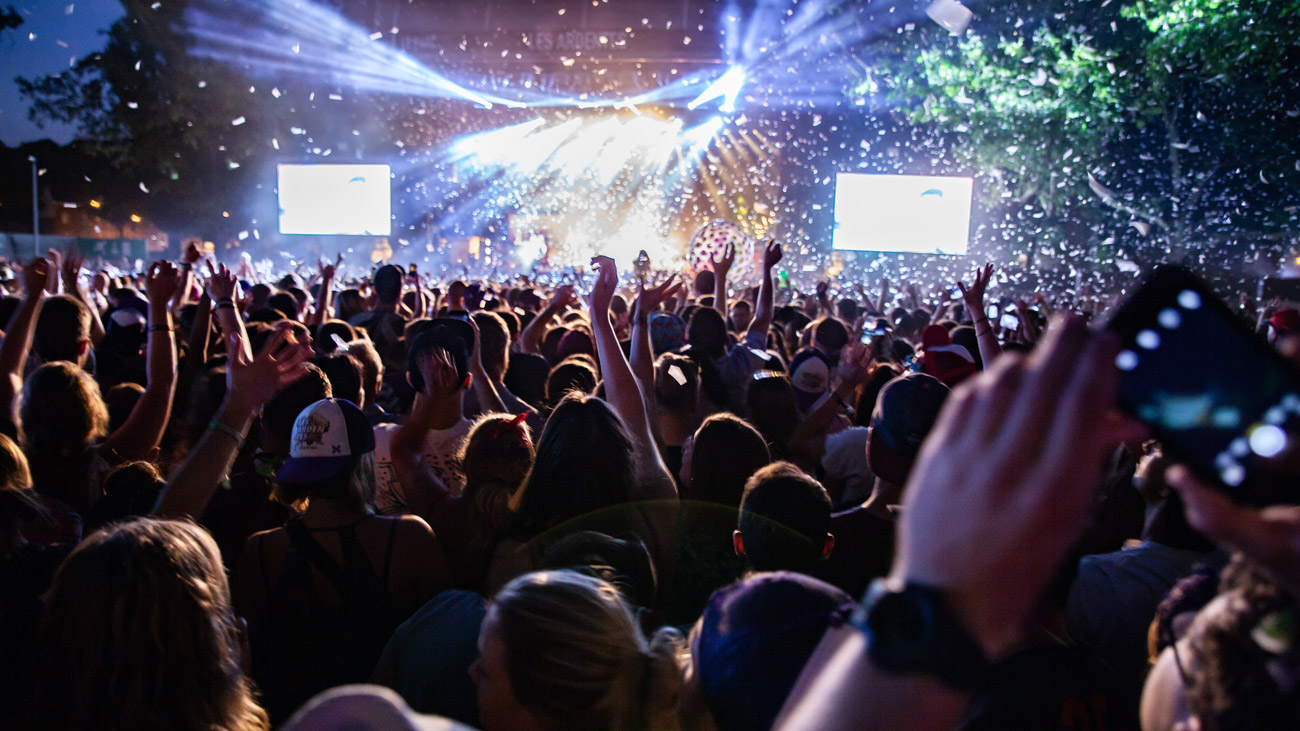
Risk assessments carried out by the Manchester Arena operators prior to the Ariane Grande concert in 2017 were nothing more than “box ticking", an inq...